Blog Center
Explore the latest stories and insights!
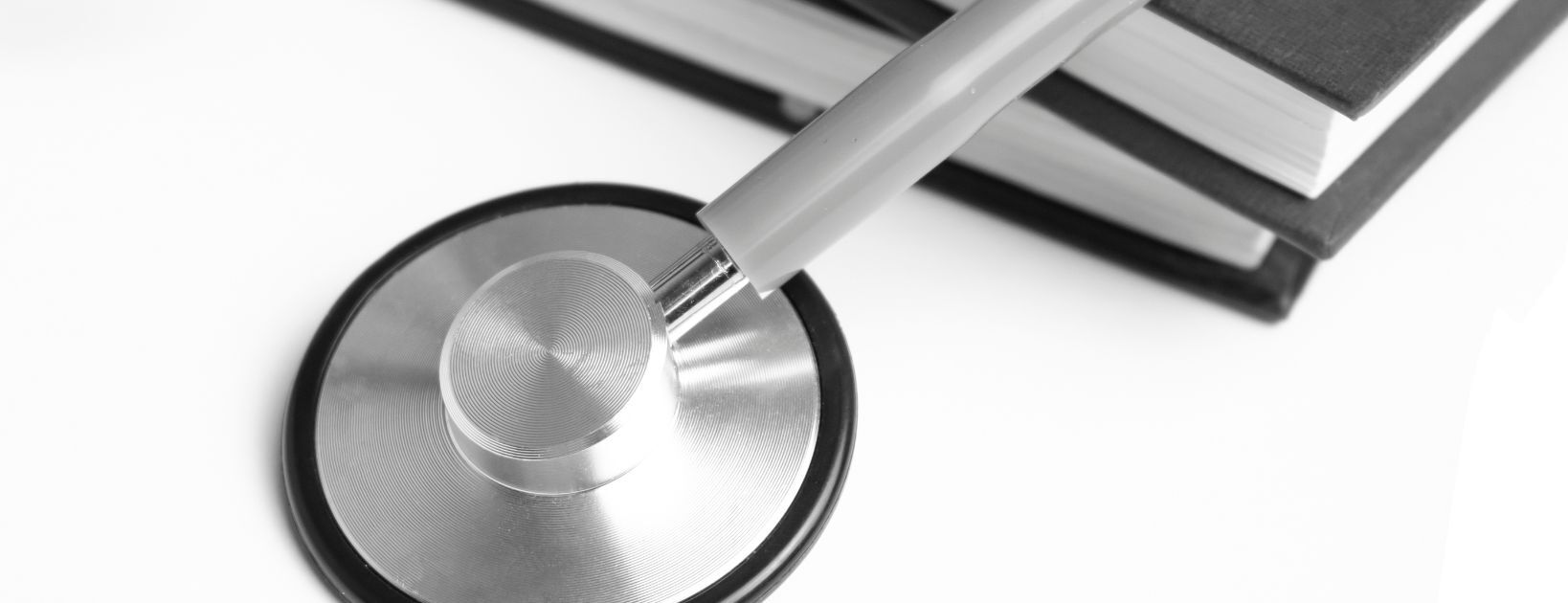
The 5 Most Important Workplace Safety Policies You Should Know About
Date: 2022/09/29
OSHA | 4.06 MIN READ
In any kind of business, the risk of injury or accident is always a possibility. In fact, the danger of harmful events occurring in the workplace is one of the main reasons why so many companies have adopted safety policies in the first place. For this reason, it’s important that you learn about some of the most important safety policies as soon as possible. The safety policy outlines what you can do to keep your employees safe at work. It also states your organization’s commitment to ensuring all staff members are safe at all times.
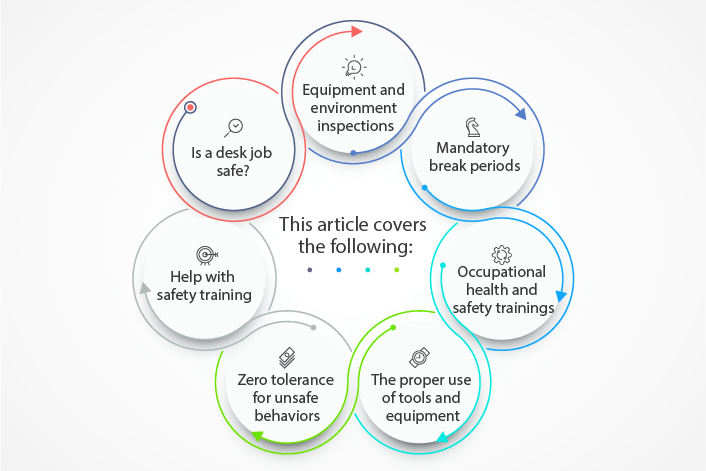
This article covers the following:
➔ Is a desk job safe?
➔ Equipment and environment inspections
➔ Mandatory break periods
➔ Occupational health and safety trainings
➔ The proper use of tools and equipment
➔ Zero tolerance for unsafe behaviors
➔ Help with safety training
Is a desk job safe?
Many of us think that if we have a desk job we are free from all kinds of dangers. But in reality, that’s not true. Even if you have a desk job and don’t regularly face threats to your physical well-being, the risk of injury at work is still present. The Bureau of Labor Statistics estimates that more than 5 million non-fatal work injuries occurred in the U.S. in 2016 alone—and those are only the incidents that were reported. The truth is that there are countless ways for employees to get hurt at work every single day, from cuts and falls to exposure to hazardous chemicals and more. However, you can keep yourself safer by following these five essential workplace safety policies:
Equipment and environment inspections
One of the most important workplace safety policies you should enforce is regular equipment and environment inspections. This will not only help you spot dangerous conditions before someone gets hurt, but it will also let you know when certain pieces of equipment or machinery may need to be replaced. When conducting these inspections, make sure to check everything from stair rails to stairwells, ladders and scaffolding, electrical equipment and power sources, hazardous chemical storage and usage areas, and more. You should also make sure workers are wearing appropriate personal protective equipment (PPE) when they are in areas where they are at risk of exposure to chemicals. To help ensure the safety of everyone in the workplace, take periodic photographs of the area and keep a log of all inspections that have been conducted. You should also keep a record of all equipment that has been purchased and installed in the workplace.
Mandatory break periods
Repetitive movement injuries are one of the most common types of work injuries, and they can often be extremely serious. One way to help prevent these types of injuries is by enforcing mandatory break periods during work hours. These don’t have to be long—10 to 20 minutes is usually more than enough time to get the job done. During this time, the employee should take a break from the repetitive motion that caused the problem in the first place. This will allow the muscles a chance to relax and get some much-needed blood flow. It’s best not to engage in these activities in front of a computer, where you may be tempted to continue working. Instead, take the break time as a chance to get away from the computer and stretch your muscles. You can also take this time to walk around the office or building to get your blood flowing again. This will help to prevent carpal tunnel syndrome and other repetitive movement injury symptoms.
Occupational health and safety trainings
Another important workplace safety policy is occupational health and safety trainings. These trainings should be offered to all employees, not just those who work in areas that are commonly associated with injuries. Some of the topics that should be included in these trainings include first aid, CPR, fire safety, chemical safety, electrical safety and more. You should also make sure to include information about the correct way to lift heavy objects and how to avoid musculoskeletal disorders (MSDs), such as carpal tunnel syndrome. According to OSHA, MSDs are the most common type of workplace injury and account for nearly 36% of all work-related injuries.
The proper use of tools and equipment
Using tools and equipment the proper way can help you prevent a wide variety of workplace injuries. Make sure workers know how to use all tools and equipment properly before they start using them. If they are using a new tool or piece of equipment, require workers to attend training before they use them. You should also inspect all equipment and tools regularly for signs of wear or damage and have them repaired or replaced as needed. Using the ergonomically correct tools also helps reduce the risk of MSDs. Additionally, you should make sure all equipment is in good working order and has the appropriate safety features, such as guards, brakes and lights. Keep a record of all equipment purchased for the workplace and install labels on all pieces of equipment that are especially hazardous.
Zero tolerance for unsafe behaviors
Another important workplace safety policy is zero tolerance for unsafe behaviors. This means that you don’t just have a policy that workers must follow—you also have a policy for what happens when someone breaks that policy. Make sure everyone in the workplace knows what the consequences of breaking the rules are and that they are enforced as soon as they are broken. For example, make it clear that anyone who fails to wear PPE when they are in a chemical-heavy area will be terminated immediately. It’s also important to make sure everyone in the workplace has a safe place to voice their concerns and report violations or mistakes that have been made. But this should be confidential, so that workers know they can report violations without fear of being fired or treated unfairly.
Need help with safety training?
It can be hard to manually incorporate all of these into workplace practices and then inspect for proper implementation of it. But things get easier with compliance training solutions. As a top player in the compliance field, Smart Training offers a wide range of safety courses specifically developed for each industry. You can buy individual courses or get a subscription to have access to courses with packages.
Subscribe to Our Blog
You may also like